High Temperature Elastomers in Oil & Gas
David Simpson posted on November 11, 2014 | Comment | 11699 views
David Simpson posted on November 11, 2014 | Comment | 11699 views
Elastomers are used all over the Oil & Gas industry. They facilitate downhole packers sealing, they allow progressing cavity pumps (PCP) to work, and they provide sealing materials for valves and equipment on the surface.
Frequently the root cause of a failure is that an inappropriate elastomer was selected (or defaulted). The elastomer choices seem like such a minor element of a ball valve specification that operators will simply take the default material.
The default Nitrile rubber (also known by such names as Buna-n, perbunan, acrylonitrile butadiene rubber, and NBR) is often a very reasonable choice in lower temperatures, mild fluids, and service not subject to Rapid Gas Depressurization.
When conditions are suitable, it can be a very effective and cost-effective choice. When conditions are not suitable it can be a disastrous choice.
Deep offshore and unconventional wells are forcing consideration of high temperatures, difficult chemicals, and high pressures. All of these issues require a careful evaluation of materials choices in the equipment selected. Picking a low-temperature elastomer for the stator in a progressing cavity pump located in the Barnett Shale would result in run times measured in "revolutions" instead of days or weeks. Not considering winter in selecting materials for surface equipment on the Alaska North Slope or the shale fields of Northern British Columbia could easily end in disaster. The most sensitive element tends to be the elastomers used in sealing surfaces.
The basic building block of all plastics is the "monomer". Monomers are complex structures of carbon compounds that have the ability to bond with other monomers (both of the same species and to a limited extent to other species) to make "polymers". Materials are called "plastic" if all of the polymer chains are similar to each other and each strand is distinct from other strands.
When the polymers "cross link" the plastic becomes an elastomer. Cross linking was first done by Charles Goodyear (1839) when he "vulcanized" natural rubber (NR) by adding sulfur to improve the performance of rubber products. When polymers cross-link, their structure resembles a fishnet more than a rope and there is room for the bulk structure to flex without breaking.
The chemical bond at the cross link is the key to temperature and chemical performance. NBR cross links typically happen at hydrocarbon sites (i.e., CnHm). Fluoroelastomers (FKM in the U.S., FPM in ISO documents) is created by replacing most of the hydrogen atoms in the hydrocarbon elements with fluorine atoms. Perfluoroelastomers (FFKM or PFE) have replaced all of the hydrogen atoms in the hydrocarbon elements with fluorine.
Elastomer performance with increasing temperature
Elastomer performance with increasing temperature
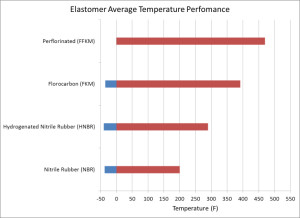
Elastomer Temperature Performance
As temperatures increase, users of products with elastomers in them progress from NBR to FKM and finally to FFKM. Each step up this ladder has a significant cost. For example, an FKM material like DyneonTM FKM from 3MTM can cost an order of magnitude more than NBR and Dyneon FFKMTM can cost another order of magnitude more than their FKM product (i.e., 100 times more expensive for the same end-product as an NBR version).
The high cost of FFKM material limits its use to applications where less expensive products would likely fail since many of the other performance characteristics are very similar at lower temperatures.
Chemical resistance of elastomers
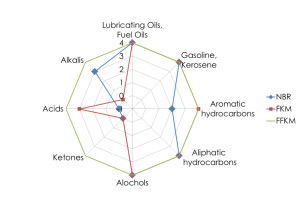
Elastomer chemical performance
Different classes of elastomers respond to solvents differently. For example natural rubber quickly becomes inelastic in oxidizing chemicals, oils, petroleum, etc. Nitrile does better in oils and other petroleum products, but still has a tendency to swell and is not good in acids or ketones. FKM material does well with most hydrocarbons, but is generally not tolerant of alkalis. FFKM material shows its high value to support its very high cost in being able perform properly in all of the solvents that typically cause problems for elastomers.
Resistance to rapid gas decompression
ISO 23936-2, NORSK M-710, and API 6A focus on testing and material performance standards when a defined mix of methane, nitrogen, or hydrogen sulfide with carbon dioxide in specified proportions is pressurized to selected pressures at defined temperatures for several days and then rapidly depressurized a number of times. The standards define very specific acceptance criteria. NBR material tends to do poorly all of the "harsh environment" tests. Some grades of FKM material do well in this test, others do poorly. FFKM does very well in this test.
How do you select an elastomer?
The end user of products containing elastomers needs to communicate pressure, temperature, and composition of fluids to the equipment manufacturer. This needs to include both nominal conditions and credible transients. Equipment manufacturers work hard to match their elastomer choices to the expected conditions because they would rather stay out of failure analysis meetings.
The options for harsh environments continuously improve, but at a cost both in terms of purchase price and a requirement for users to learn more about elastomers than we've had to know in the past. Blindly setting a policy to always use PER material for surface equipment in the fields of the Alaska North Slope would certainly cause the occasional low-temperature failure of elastomers. Being an informed consumer becomes more important as the industry moves further into deep, hot, high pressure reservoirs with difficult chemistry.
Note: 3M™ has sponsored promotion of their Oil and Gas solutions on ENGINEERING.com. They have no editorial input to this post - all opinions are mine. - David Simpson
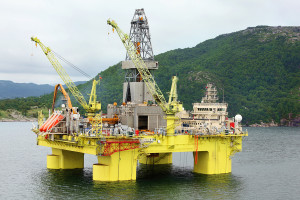
The default Nitrile rubber (also known by such names as Buna-n, perbunan, acrylonitrile butadiene rubber, and NBR) is often a very reasonable choice in lower temperatures, mild fluids, and service not subject to Rapid Gas Depressurization.
When conditions are suitable, it can be a very effective and cost-effective choice. When conditions are not suitable it can be a disastrous choice.
Deep offshore and unconventional wells are forcing consideration of high temperatures, difficult chemicals, and high pressures. All of these issues require a careful evaluation of materials choices in the equipment selected. Picking a low-temperature elastomer for the stator in a progressing cavity pump located in the Barnett Shale would result in run times measured in "revolutions" instead of days or weeks. Not considering winter in selecting materials for surface equipment on the Alaska North Slope or the shale fields of Northern British Columbia could easily end in disaster. The most sensitive element tends to be the elastomers used in sealing surfaces.
The basic building block of all plastics is the "monomer". Monomers are complex structures of carbon compounds that have the ability to bond with other monomers (both of the same species and to a limited extent to other species) to make "polymers". Materials are called "plastic" if all of the polymer chains are similar to each other and each strand is distinct from other strands.
When the polymers "cross link" the plastic becomes an elastomer. Cross linking was first done by Charles Goodyear (1839) when he "vulcanized" natural rubber (NR) by adding sulfur to improve the performance of rubber products. When polymers cross-link, their structure resembles a fishnet more than a rope and there is room for the bulk structure to flex without breaking.
The chemical bond at the cross link is the key to temperature and chemical performance. NBR cross links typically happen at hydrocarbon sites (i.e., CnHm). Fluoroelastomers (FKM in the U.S., FPM in ISO documents) is created by replacing most of the hydrogen atoms in the hydrocarbon elements with fluorine atoms. Perfluoroelastomers (FFKM or PFE) have replaced all of the hydrogen atoms in the hydrocarbon elements with fluorine.
Elastomer performance with increasing temperature
Elastomer performance with increasing temperature
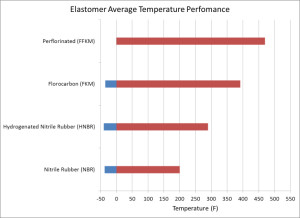
The high cost of FFKM material limits its use to applications where less expensive products would likely fail since many of the other performance characteristics are very similar at lower temperatures.
Chemical resistance of elastomers
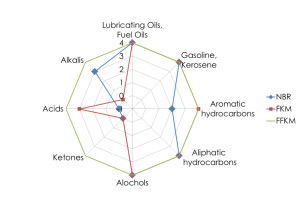
Resistance to rapid gas decompression
ISO 23936-2, NORSK M-710, and API 6A focus on testing and material performance standards when a defined mix of methane, nitrogen, or hydrogen sulfide with carbon dioxide in specified proportions is pressurized to selected pressures at defined temperatures for several days and then rapidly depressurized a number of times. The standards define very specific acceptance criteria. NBR material tends to do poorly all of the "harsh environment" tests. Some grades of FKM material do well in this test, others do poorly. FFKM does very well in this test.
How do you select an elastomer?
The end user of products containing elastomers needs to communicate pressure, temperature, and composition of fluids to the equipment manufacturer. This needs to include both nominal conditions and credible transients. Equipment manufacturers work hard to match their elastomer choices to the expected conditions because they would rather stay out of failure analysis meetings.
The options for harsh environments continuously improve, but at a cost both in terms of purchase price and a requirement for users to learn more about elastomers than we've had to know in the past. Blindly setting a policy to always use PER material for surface equipment in the fields of the Alaska North Slope would certainly cause the occasional low-temperature failure of elastomers. Being an informed consumer becomes more important as the industry moves further into deep, hot, high pressure reservoirs with difficult chemistry.
Note: 3M™ has sponsored promotion of their Oil and Gas solutions on ENGINEERING.com. They have no editorial input to this post - all opinions are mine. - David Simpson
No comments:
Post a Comment